Barcode Blues : comment les problèmes de codes-barres peuvent paralyser la chaîne d’approvisionnement automobile
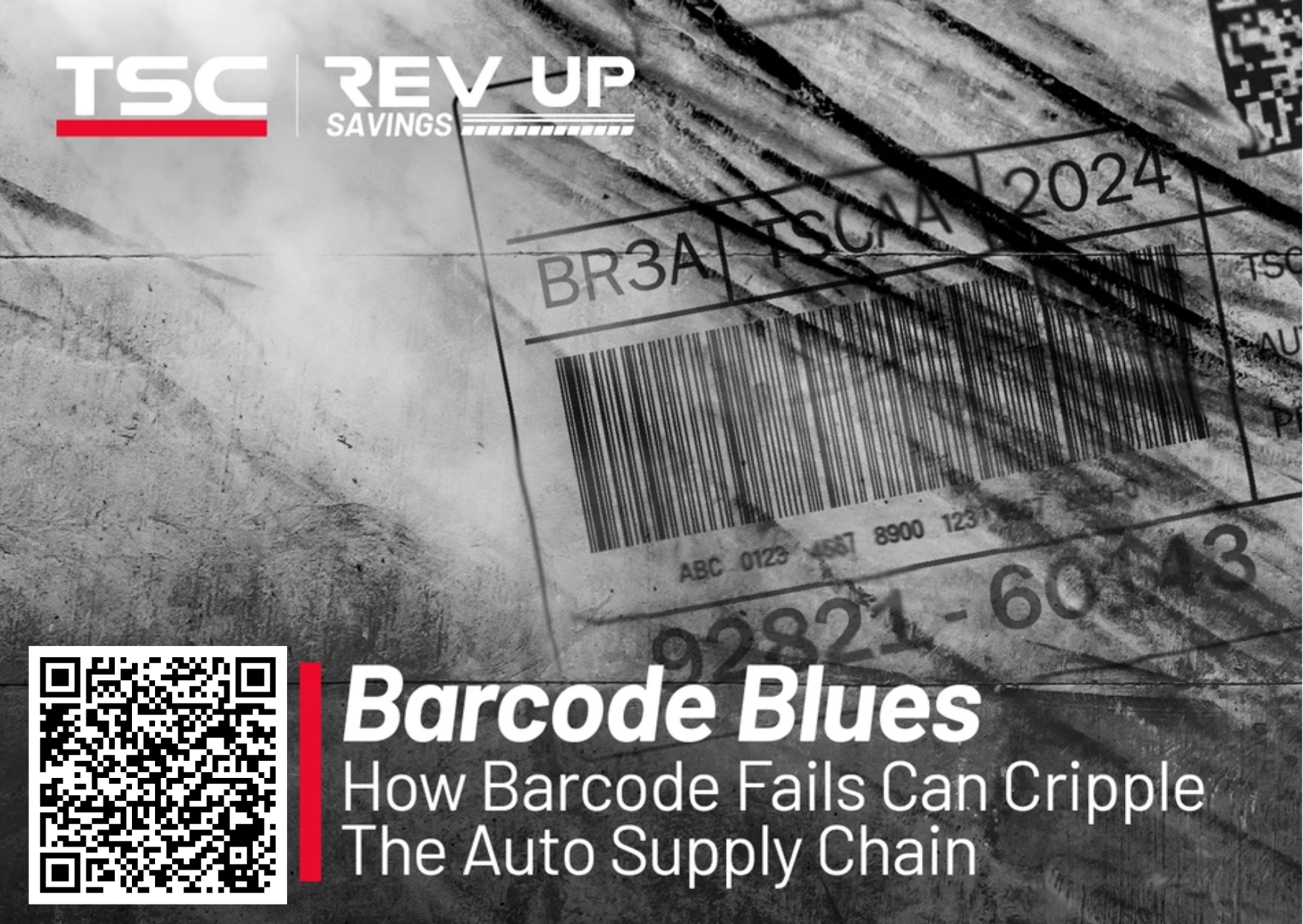
Dans tout processus efficace ou semi-automatisé, les erreurs peuvent perturber considérablement les flux de travail et s’avérer coûteuses à résoudre. Plus précisément, dans le cas des problèmes de codes-barres dans la chaîne d’approvisionnement automobile, les conséquences sont les suivantes :
- Pertes du transporteur pendant l’envoi et colis non distribuables
- Emplacements inconnus des marchandises reçues
- Niveaux de stocks incorrects dans la base de données ERP des clients
- Rétrofacturations des clients ou frais
- Défaillances des équipements automatisés reposant sur la vision artificielle qui mettent en péril les flux de travail
- Plaintes des clients entraînant une baisse de la satisfaction et de la fidélisation des clients
- Temps d’arrêt et de reprise nécessaires pour résoudre les problèmes d’étiquetage
- Absence de traçabilité et de limitation des problèmes restreints de non-conformité de fabrication
La bonne nouvelle, c’est que la plupart de ces problèmes peuvent être réduits par l’utilisation d’un système d’inspection des codes-barres utilisant une vérification à 100 %. Non seulement la vérification des codes-barres empêche l’émission de codes illisibles, mais elle permet également à un ingénieur qualité de comprendre pourquoi le code est défaillant et d’identifier le besoin de maintenance préventive ou d’autres interventions nécessaires avant que des effets plus graves ne se produisent. Avec le bon système, vous pouvez fournir des cartes de contrôle pour toutes vos imprimantes sans engager d’ingénieurs supplémentaires.
Quelles sont les causes de scans invalides ou de codes illisibles ?
Les normes ISO 15415 et 15416 prévoient un système de classement pour la symbologie 1D et 2D, respectivement, qui permet aux enquêteurs de connaître précisément la cause des défaillances des codes-barres. En général, ces défaillances sont liées aux paramètres et à la configuration de l’imprimante, à la conception et au code de l’étiquette, ou à la qualité du support et du ruban. Pas besoin d’avoir inventé l’eau chaude pour savoir précisément où chercher les problèmes de qualité. Les codes non scannables peuvent être dus à l’un des paramètres indiqués dans le tableau 1 et chacun d’entre eux est automatiquement mesuré et signalé pour chacun des 50 codes-barres/étiquettes maximum utilisant l’ODV-2D.
Tableau 1. Paramètres ayant un impact sur la qualité des codes-barres selon les normes ISO 15415/15416
Paramètres | Types de codes | Description | Causes et interventions |
Décoder | 1D/2D | Lecture de codes-barres (réussite/échec) | Bavure de l’encre, température de chauffe incorrecte |
Contraste des symboles | 1D/2D | Différence de contraste entre les barres blanches et noires | Pression inégale de la tête d’impression, tête d’impression encrassée, étiquettes de mauvaise qualité, problèmes de ruban |
Réflexion min. | 1D | Mesure de l’obscurité des barres noires | Qualité médiocre du ruban du fournisseur, température de chauffe de la tête d’impression |
Contraste min des bords | 1D | Contraste entre les barres/espaces adjacents | Pression inégale de la tête d’impression |
Modulation | 1D/2D | Variation de la largeur et de la position des barres | Problème de source de données, de format d’étiquette ou d’étalonnage |
Défauts | 1D | Recherche d’irrégularités dans le schéma | Tête d’impression ou rouleau de platine encrassés |
Décodabilité | 1D | Dans quelle mesure le schéma est-il proche des dimensions idéales ? | Mauvaise image de code-barres, violations de la zone de silence |
Dommages de schéma fixe | 2D | Dommages aux points de repère ou aux zones de silence définies par la symbologie | Froissement du ruban, défauts de l’étiquette, saleté ou débris, problèmes de conception de l’étiquette |
Non-uniformité axiale | 2D | Mesure de l’asymétrie dimensionnelle entre les axes X et Y | Problèmes de compression ou d’émulation d’images |
Non-uniformité de la grille | 2D | Mesure de la distorsion ou de l’étirement de la grille | Corruption du modèle d’étiquette |
Correction d’erreur inutilisée | 2D | Mesure de la redondance nécessaire pour continuer à lire le code | Indique la présence de défauts ou de combinaisons d’autres paramètres |
Classer 100 % de vos étiquettes en fonction de ces dimensions peut sembler une tâche ardue, mais nous avons automatisée cette action pour vous dans nos systèmes d’inspection de codes-barres par vérification des données en ligne (ODV). Le dernier système en date est notre ODV-2D, une solution entièrement intégrée qui permet d’imprimer, de vérifier et de valider les codes-barres 1D et 2D. Plus précisément, ce système :
- Classe jusqu’à 50 codes-barres par étiquette, y compris les symbologies 1D (Code 39, Code 93, Code 128, UPC/EAN et 2 D Datamatrix (Carré, Rectangle), PDF 417, QR) les plus courantes
- Classe pendant l’impression jusqu’à 8 pouces par seconde (IPS)
- Peut classer des étiquettes et des formulaires jusqu’à 6,5" de large
- Peut résoudre des caractéristiques de dimension X jusqu’à 10 (mils) ou environ 250 microns.
- Surimprime les étiquettes de mauvaise qualité et réimprime automatiquement en fonction de seuils définis par votre équipe.
L’unité ODV-2D, d’un prix abordable, s’installe sur les imprimantes T8000 ou T6000e et peut être achetée préinstallée pour faciliter l’étalonnage. C’est le premier système qui classe les codes-barres selon les normes ISO 15415, 15416 et 15426 et qui stocke un rapport détaillé de chaque transaction à des fins d’audit, apportant ainsi à vos clients la preuve de vos normes de haute qualité.
Histoire d’une réussite : Fabrication de motos
Un fabricant de pièces automobiles étiquetait de petits composants avec plusieurs codes-barres 2D afin de partager de façon compacte les données de traçabilité en aval avec les clients de niveau 1. Les données étaient difficiles à lire en aval, ce qui entraînait des retours de produits et une faible satisfaction des clients. En utilisant ODV-2D sur une imprimante T6000e, nous avons révélé de multiples violations de la zone de silence qui peuvent entraîner un décodage médiocre et incohérent. Nous les avons aidés à ajuster la taille des codes-barres dans la conception de leurs étiquettes et nous les avons équipés de systèmes ODV-2D pour garantir que même les codes Data Matrix de petite taille puissent être classés jusqu’à des caractéristiques de 250 microns, ce qui permet d’économiser du temps et de l’argent précieux.
En savoir plus
Vous voulez aller plus loin ? Découvrez comment d’autres fabricants du marché automobile utilisent la vérification des données en ligne pour réduire les erreurs, économiser de l’argent et maximiser la productivité et le temps de fonctionnement des équipements.
Nous vous montrerons en détail comment au cours des prochaines semaines, dans cette série complète d'articles intitulée « Faites des économies à plein régime ».
Vous pouvez également visiter notre page web sur les solutions automobiles à tout moment !
Nous contacter
Cliquez ici pour prendre rendez-vous pour une consultation gratuite.